Why Are Physical Assets Underperforming?
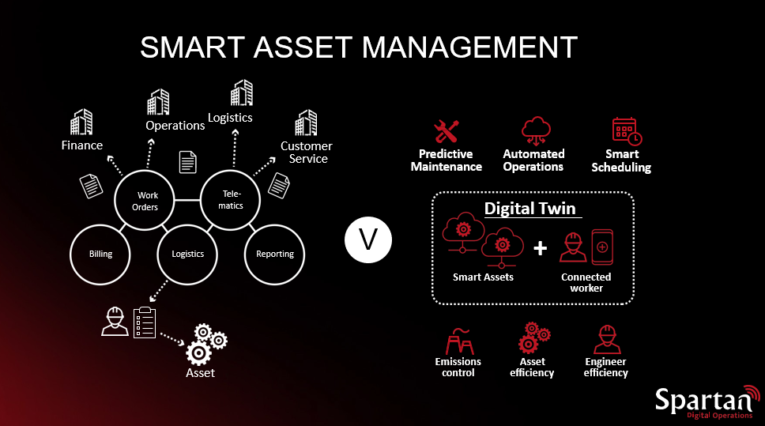
Optimising the return on investment of physical assets is proving increasingly difficult across a range of industries:
Oil and Gas producers in the UK North Sea have seen plant and equipment reliability drop by 14% annually, while operations and maintenance increased by 3%.
The cost of plant and equipment in civil engineering construction projects can range from 25% to 40% of the total project costs. Equipment failure and logistics delays will result in considerable time and budget overruns.
The cost of operating and maintaining an offshore wind turbine is 30% of the total lifetime cost, and each turbine requires six technician visits on average per-annum.
Many organisations are now turning to the latest Asset Performance Management (APM) solutions to get the most from their assets. Before they can do so, however, they must understand the barriers that are holding them back.
Barriers to digital innovation in asset-centric companies
There are five unique challenges facing companies that rely on physical assets to generate profit:
Laws of physics
The physical nature of plant and equipment constrains the potential return on investment. Wear and tear impacts the physical fabric of machinery, especially in challenging environments such as a construction site in a northern hemisphere winter or a North Sea platform. Any digital innovation must reduce the operations and maintenance teams’ burden and demonstrate a high return on investment.
Engineering culture
Executives in asset-centric companies are often engineers by education and trade who have risen through the ranks to leadership positions. Therefore, the engineering mindset tends to dominate the organisation’s culture: a preference for rigorous analysis and process over quick decisions and agile projects; a premium on finding and validating the ‘perfect’ solution up-front.
Reluctance to change
Managing physical plant and equipment in a complex environment is inherently dangerous. The consequences of failure are often threatening to life, the environment and even the organisation’s existence. Regulations have developed at every level of local, national and global government to manage the risks. An unintended consequence is that people are rewarded not for driving innovation but for exercising caution and minimising change.
Dependence on third parties
Managing a large civil engineering project requires the successful coordination of many third parties. Implementing a significant process change can require re-negotiating the technical, process and even financial interfaces with key suppliers and partners.
Global operation
Most asset-centric companies operate in multiple countries. The legal, technical and commercial environments in these countries can vary significantly. Access to basic internet connectivity can be challenging, data ownership laws can constrain the possibilities of Artificial Intelligence, and company silos can foster a ‘not invented here’ barrier to global adoption.
The pandemic has brutally exposed inefficient asset management and supporting supply chain processes. There is an urgent need to use digital technology to innovate new APM processes that reduce maintenance costs and increase equipment availability.
Asset centric companies need to align the engineering culture that has delivered success to date with the opportunity to transform their APM strategy and ensure future profitability.
This blog is an excerpt from our “Guide to Asset Performance Management for Oil & Gas Operators“. Download the full guide for more insights, such as “What Does Excellent Asset Management Look Like?“.