APM in Action: Reducing Emissions While Improving Operational Efficiency
In the wake of the pandemic, equipment rental companies are faced with more demanding customers and fewer workers to manage them. At the same time, there is a growing awareness of the environmental impact of the construction sector, and the EU has set the industry a target of net neutral emissions by 2050.
Customers are asking rental companies to support a diverse range of new needs, from reducing CO2 emissions and increasing fuel efficiency to improving excavator drivers’ productivity. Rental companies are looking for innovative ways to deliver world-class customer service and increase operational efficiency with a leaner workforce and a lower cost base.
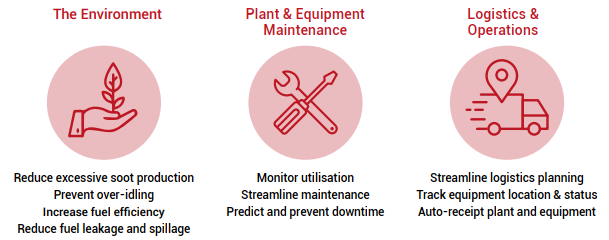
Using APM to automatically monitor, predict, and react to changes in equipment and operations data opens a wide range of business opportunities.
APM is like a 24x7x365 radar system, constantly looking out for ways to improve customer service, increase plant and equipment performance, reduce emissions, and streamline logistics and service processes.
APM has built-in algorithms to predict and prevent excessive soot production, inefficient fuel use, fuel spillage, fuel leakage, and over idling to protect the environment.
To improve plant performance, APM will auto-monitor and warn of underutilisation, overutilisation, wrong sizing and contract breach (e.g., time of day, running hours or location breaches).
APM will also reduce the cost of over and under maintaining equipment. Reactive breakdown alerts from equipment are automatically ranked by severity, with maintenance work orders raised automatically or on approval by a fleet manager. APM continuously monitors equipment condition, and combined with equipment maintenance history, recommends maintenance work based on current or predicted equipment condition.
Finally, APM supports the planning and logistics of equipment movements and equipment servicing. It provides a real-time map view of plant and equipment, filterable by custom, project and equipment status. APM uses geo-fences to auto-receipt equipment at customer locations, enhance customer service, and provide a valuable track and trace capability.
APM also auto-receipts plant and equipment at the receiving depot, speeds up the turnaround process and improves equipment visibility at the depot. The system also groups equipment maintenance by priority and location, helping service manager plan cost-effective maintenance campaigns and increase the wrench time of service engineers.
Modern APM solutions, designed for the equipment rental market, leverage Artificial Intelligence and advanced automation to transform rental operations and the services that rental companies can provide to end customers.
APM makes rental companies more efficient, rental customers more productive, and helps save the planet.
This blog is an excerpt from our “Guide to Asset Performance Management for Equipment Rental”.
Download the complete guide for more insights, such as “Asset Performance Management at Every Level“.
Tags: APM, Equipment Rental